The petrochemical industry is highly regulated and has an extreme focus on safety. Having a trusted partner with expertise in moving these essential materials can help the companies that produce and provide these products while helping their customers gain a competitive advantage through domestic and global expansion.
Technology is key to moving chemicals safely
Chemicals are critical for various industries, including manufacturing, agriculture, pharmaceuticals, and construction. The production, transportation, and use of hazardous materials are essential to the global economy. The increased harmonization of regulations, better data, new technology, and cooperative efforts between shippers, carriers, tank car builders, and governments influence safe transport practices for hazardous materials.
Having the expertise and the technology to help determine the best way to move these essential components to their destination can ensure the product arrives safely and on time. What is the best way to achieve the optimal transportation for these critical ingredients? The two primary modes of overland transport are rail and road freight. The answer is not likely one or the other, but how do the modes complement each other to carry what is needed with minimal risk and at the lowest cost?
When to use rail vs road
It makes sense to use rail to move larger, heavier shipments. Rail transportation of hazardous materials in the United States is recognized to be the safest land-based method of moving large quantities of chemicals over long distances. (U.S. Department of Transportation Federal Railroad Administration) Recent statistics show that the rail industry’s safety performance, as a whole, is improving. In particular, the vast majority of hazardous materials shipped by rail tank car every year arrive safely and without incident, and railroads generally have an outstanding record in safely moving shipments of hazardous materials.
Accidents happen, but rail shipments are generally the safer option
However, incidents such as the February 2023 derailment of a Norfolk Southern train in Ohio have brought a renewed focus on rail safety, with U.S. lawmakers and public officials calling for reforms to improve safety standards. About 20 cars involved in the incident contained hazardous materials. Several days after the derailment, public officials and Norfolk Southern leadership decided to vent five cars out of concern that they could explode because of the chemical reactions inside them. This generated a large amount of smoke lingering over the incident site, causing worry in the community about long-term effects.
With that said, according to the Association of American Railroads, more than 99.9% of hazmat shipments moved by rail reach their destination without incident. The risk of a rail accident is around 40 times lower than for road transport. This results in a significantly lower failure rate for shipments. And with the few accidents on rail, there is also less risk of total loss, which frequently occurs after accidents with trucks on the road.
Moving chemicals by rail means planning ahead
Moving chemicals by rail requires planning. Trains must adhere to timetables and cannot deviate to accommodate an unexpected delivery order. In addition, a train can only deliver to locations that handle rail sidings, so trucks are still needed for door-to-door deliveries.
Moreover, the rail infrastructure limits the flexibility of moving chemicals by train. Only as many trains can run as the rail network allows. This can lead to unwanted waiting times. As the infrastructure in many countries is limited and outdated, urgently needed maintenance work on the rail network adds to the expansion measures in many places. Repair work further restricts the already scarce rail capacities and extends transport times, while unexpected damage to bridges or signal boxes can lead to train cancellations.
However, using standardized containers makes transferring from rail to road carriers easy, eliminating the need for time-consuming reloading. The containers or trailers are simply lifted from the train onto the truck or vice versa. Transloading between freight trains and container ships is also quick if the port infrastructure is adequate. The intermodal capabilities support transportation when not every industrial park has a rail connection.
Railroads move the chemicals that make modern life possible
While there have been some incidents of derailments, continuous industry and government improvements in rail equipment, tank car and container design and construction, and inspection and maintenance methods have reduced derailments, spills, leaks, and casualties while the volume of traffic increases. Freight railroads moved 2.3 million carloads of plastics, fertilizers, and other chemicals in 2022. (Source –AAR Chemicals Fact Sheet)
Railroads safely, efficiently, and cost-effectively transport the chemicals that make modern life possible. These include moving fertilizers to farmers, plastic resins to auto parts producers, caustic soda to pulp and paper manufacturers, and countless other chemical products to intermediaries and end users throughout the U.S. and the world.
With highly-regulated operations and stringent safety measures, railroads efficiently move crucial materials and help chemical customers compete in the global marketplace while supporting business expansion.
Have confidence in shipping your chemicals safely
Having a partner with the knowledge and the technology to transport these essential products, whether on the road or rail, efficiently and safely, while meeting all regulatory compliance requirements, helps companies gain a competitive advantage in a complex global shipping environment. E2open Transportation Management, coupled with CLX Logistics experience in the chemical industry, provides deep domain expertise and best-in-class transportation solutions with speed and efficiency.
Learn more about how e2open and CLX can help you move chemicals safely.
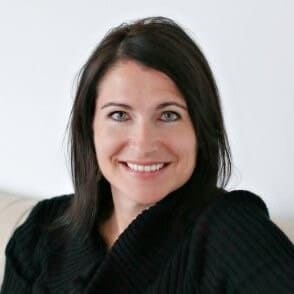
Author
Nicole Hudson
As a Director of Product Marketing at e2open, Nicole is focused on Transportation and Logistics applications. Over her 20+ year career, she has held various positions in product management and product development for supply chain and logistics companies, including JDA and BluJay Solutions. She joined the product marketing team at e2open in 2022 with the BluJay acquisition. Nicole currently lives in WI and enjoys attending her kids’ volleyball and basketball games and traveling in her spare time.