Supply | Recall Management
Product Recall Management Helps Protect Your Brand with Defect Detection and Traceability
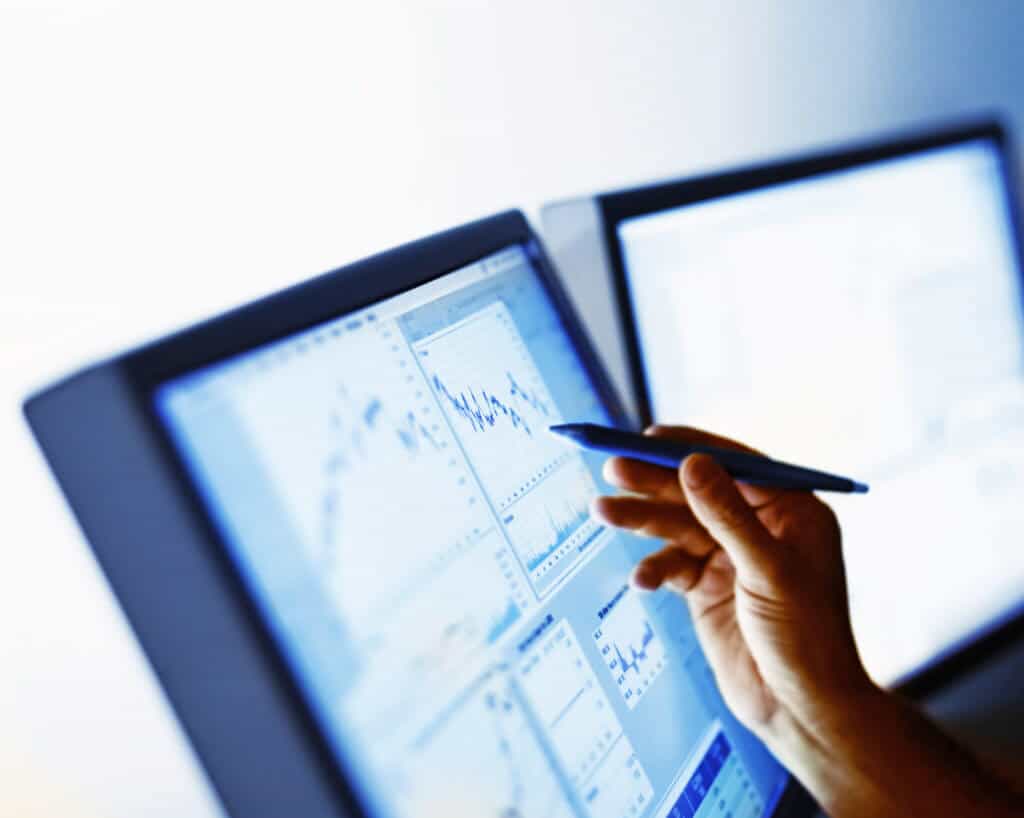
Automatically detect quality issues and effectively manage recalls
Protect your brand by quickly pinpointing quality issues and taking decisive action. With e2open Recall Management, you can analyze goods for potential failures, identify the source of any defects, locate and quarantine the affected goods, and respond quickly with surgically precise recalls.

Defective goods can lead to damaged brands
Brand owners lack the speed and visibility to detect issues quickly
The continued rise in outsourcing and the variability of raw materials has led to an increasing number of defective goods. When you add in the complex nature of global supply chains, it becomes obvious that identifying quality issues can feel like finding a needle in the figurative haystack. Unfortunately, the inability to identify defective goods and respond quickly can lead to costly recalls and brand damage—and even danger to consumers.
Identify defects, locate the source, respond rapidly
Recall Management gives you the ability to pinpoint the root cause of defects quickly, so you can prevent future recalls.
Related applications
Customers
Fast, efficient recalls